What is the hardest material on Earth? Traditionally, because of its extreme hardness, diamond is used as a cutting material in a multitude of fields, from aerospace engineering to geothermal energy. Recently, using ultra-high pressures and temperatures, scientists have created a new form of diamond, which is now the hardest material known to humankind.
Dr. Guodong (David) Zhan and Timothy Eric Moellendick at Saudi Aramco, alongside Dr. Duanwei He at Sichuan University, are the scientists behind this record-breaking substance, which will serve as an “indestructible” cutting and drilling material.
Hard Materials
Diamond is the hardest naturally occurring material on Earth, comprising carbon atoms that are tightly bonded together in an infinite lattice. Its extreme hardness makes diamond an ideal material for cutting and drilling technologies.
However, natural diamonds can only be found around 100 miles below Earth’s surface, where the extremely high pressures and temperatures allow the material to form naturally. Rarely, diamonds can be found closer to Earth’s surface, when a deep volcano brings them up to where they can be mined.
Although diamond is the hardest natural material on Earth, it can still sometimes fracture and wear down when drilling through very hard rock formations. Therefore, much research has been dedicated to creating synthetic diamonds that have increased impact and wear resistance.
In the 1970s, the first polycrystalline diamond drill bit was created, using high-pressure and high-temperature technology. “Polycrystalline” means that there are many individual diamond crystals that are randomly oriented with respect to one other, leading to a material that is more resistant to impact and wear than a single crystal of diamond.
Currently, the “polycrystalline diamond compact” is the most commonly used material for creating cutting and drilling materials, such as those used in aerospace, geoscience, geothermal energy, and oil and gas drilling. As well as its extreme hardness and resistance, polycrystalline diamond compact also has high thermal conductivity, which prevents too much heat from building up at the cutting site.
Although this material has been greatly enhanced over the last few decades, there is still much room for further improvement. This main weakness in current polycrystalline diamond materials stems from the fact that a cobalt catalyst is required to synthesize polycrystalline diamond, and some of this is left behind in the resulting material, reducing its performance and limiting its applications.
Cobalt residues between the individual diamond crystals can expand due to the heat generated during drilling and cutting, causing cracks to form in the material. This causes the element to fail, meaning that it needs to be replaced. Additionally, the need for other additives known as inorganic binders also reduces the performance of the resulting polycrystalline diamond compact.
To solve this issue, Dr. Guodong (David) Zhan and Timothy Moellendick at Saudi Aramco’s EXPEC Advanced Research Center, alongside their collaborator Dr. Duanwei He at Sichuan University, have devoted years to developing a new and ‘indestructible’ polycrystalline diamond compact material, by eliminating the need for catalysts and inorganic binders.
In their recent ground-breaking work, the team has invented the hardest material currently known to humankind.
“The performance of this material, the world’s strongest at this time in terms of its hardness, impact resistance, wear resistance, and thermal stability, as well as detailed material analyses, has been systematically evaluated,” says Dr. Zhan. “These results broke all industry records for wear resistance – 300% higher than the best diamond materials currently used in the industry.”
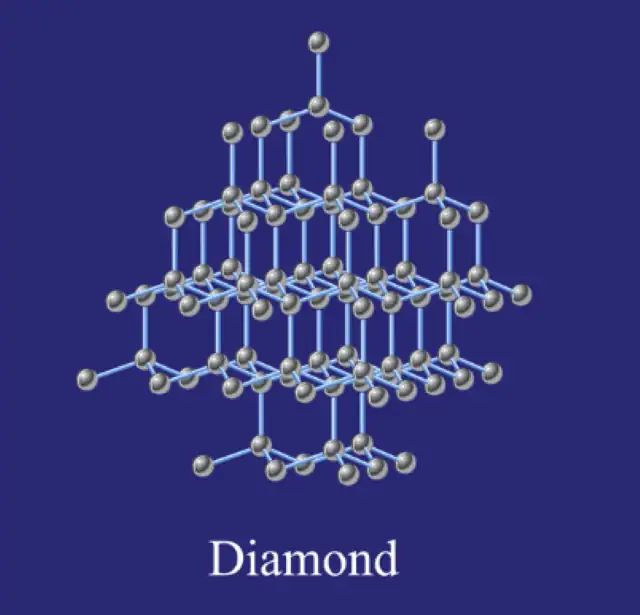
Synthesising the Hardest Material in the World
To create their record-breaking polycrystalline diamond, Dr. Zhan, Moellendick, Dr. He, and their colleagues first developed a new ultra-high-pressure, ultra-high-temperature technology, in collaboration with the Chengdu Dongwei Technology Company, which specializes in equipment that can generate such extreme temperatures and pressures. Specifically, the team’s newly developed technology uses equipment that can generate pressures of up to seven times higher and temperatures up to 800°C more than conventional methods.
The team used a fine diamond powder as a starting material. First, they heat-treated the powder at 1200°C under a vacuum and then packed the treated powder into cylindrical capsules. These capsules were then subjected to an ultra-high temperature of 2300°C and a phenomenal pressure of 16 gigapascals for 10 minutes. For comparison, a pressure of 16 gigapascals is about 150 times greater than the bottom of the deepest part of the ocean – the Mariana Trench.
The team’s ultra-high-pressure, ultra-high-temperature technology allowed them to produce polycrystalline diamond compact cutting elements without the need for a catalyst or a binder, resulting in a material with extreme hardness, resistance to impact and wear, and high thermal conductivity.
Specifically, the team found that their material had a wear resistance that is 300% higher than the best diamond materials currently used in the industry. It would usually take a decade to increase the wear resistance of polycrystalline diamond by a mere 30-50%, meaning that the team’s discovery represents a 50-year leap in the material’s development.
When attempting to measure the material’s resistance to changing shape, deformation, penetration, indentation, and scratching, the researchers actually broke parts of their hardness tester equipment.
“The new material broke all single-crystal diamond indenters, which are the world’s hardest natural materials, suggesting that the new material is too hard to be measured by the current standard single-crystal diamond indentation method,” says Dr. Zhan.
His team also found that the material is stable at temperatures of up to 1200°C in air, which is a whopping 600°C higher than the best commercial cutting materials, and 150°C higher than the best-performing experimental diamond-based materials. All of these results demonstrate that the team’s new material is the most wear-resistant, impact-resistant, hard, and thermally stable diamond in the world to date.
“Furthermore, all current research and industry development by ultra-high pressure and ultra-high temperature technology can only make miniature samples that limit their use in many potential applications. In our study, the sample dimensions of about 11 millimeters in diameter and up to 6 millimeters in thickness have been achieved for the first time,” explains Dr. He.
By comparison, most polycrystalline diamonds can only be manufactured in samples of 1 millimeter or less. The team’s material can already be manufactured in sufficiently large pieces to create cutting tools for a wide range of applications.
For this work, Dr. Zhan and Moellendick have been recognized with the E&P Special Meritorious Hart Energy Award for Engineering Innovation in 2020.
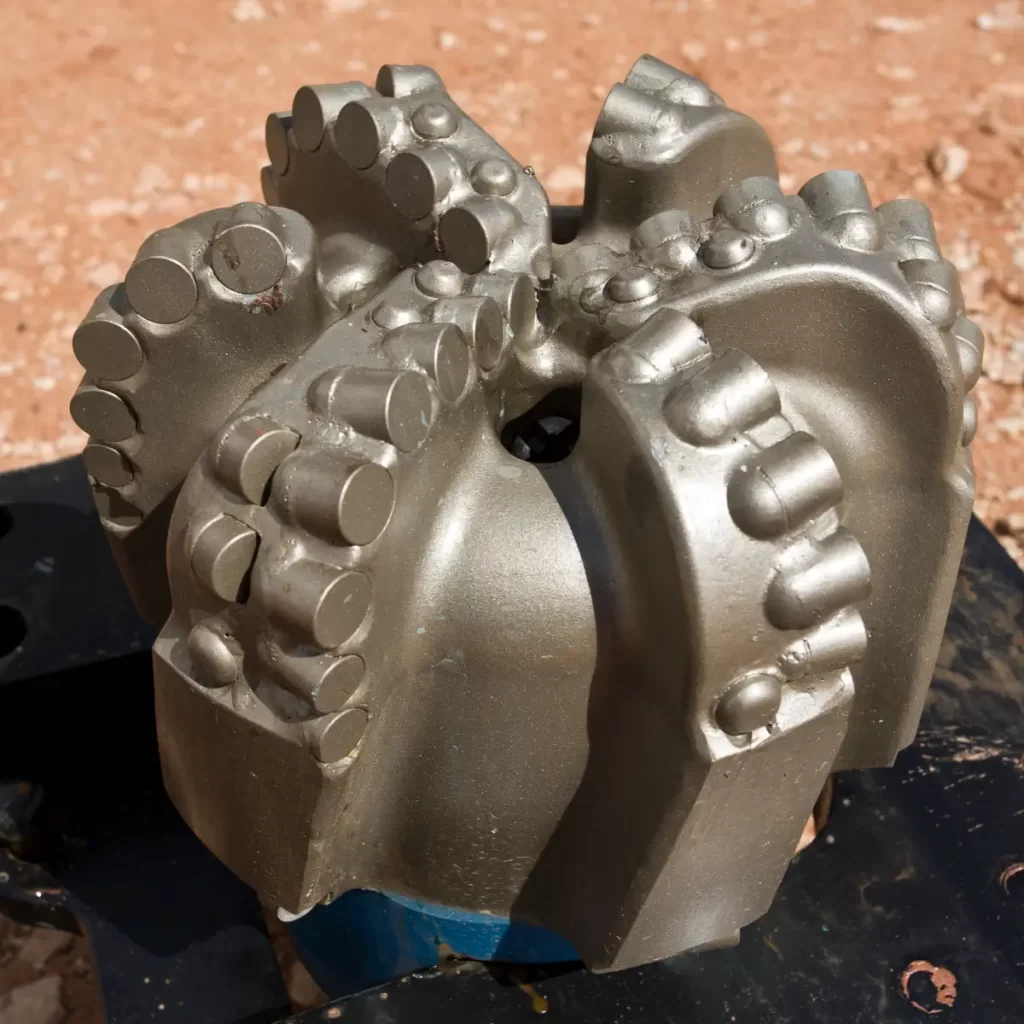
Future Applications of the Technology
“Our work represents a major breakthrough in hard materials that could open up new areas to expand many potential industrial tools and devices applications, such as Earth and aerospace exploration, fourth industrial revolution (4IR) manufacturing, all related and significant to fundamental scientific research,” says Moellendick.
One example of a future application of the team’s new polycrystalline diamond cutters is in the oil and gas industry. Polycrystalline diamond compact drill bits are key drilling tools for oil exploration and drilling. However, drilling very hard, highly abrasive, and interbedded formations is a challenge using current polycrystalline diamond compact bits, as they do not provide sufficient wear or impact resistance, nor adequate thermal stability to drill a well in a single run.
The weakness in the current technology is due to the use of a cobalt catalyst to bind the individual diamonds in the material. Therefore, the team’s ultra-strong and catalyst-free polycrystalline diamond is an ideal and game-changing drill bit technology, which delivers a significant increase in performance, durability, and economics.
Another very promising example is in the aerospace industry. Aircraft manufacture is an area that is always changing and engineers are constantly looking to improve current methods, to make aircraft safer and faster, and with improved fuel economy. The team’s material would provide these engineers with more efficient and precise cutting and grinding tools.
Furthermore, harnessing geothermal energy requires wells to be drilled deep underground, sometimes up to four or five kilometers (2.5-3 miles) below ground, to access reservoirs of hot water or steam. This hot water or steam can then be brought to the surface, where it can turn a turbine to generate renewable electricity. New and improved materials would greatly advance our ability to efficiently drill deep into the Earth’s crust, reducing the cost and time it takes to create geothermal wells.
Similarly, many geoscientists who study the composition of the Earth’s crust need high-performing drilling technology to allow them to obtain samples from deep underground. Therefore, the team’s new material could help to accelerate the field of geoscience, allowing scientists to answer key questions relating to the Earth’s formation and evolution.
Material scientists will be equally interested to utilise the world’s new hardest material for other exciting applications, such as electronic devices.
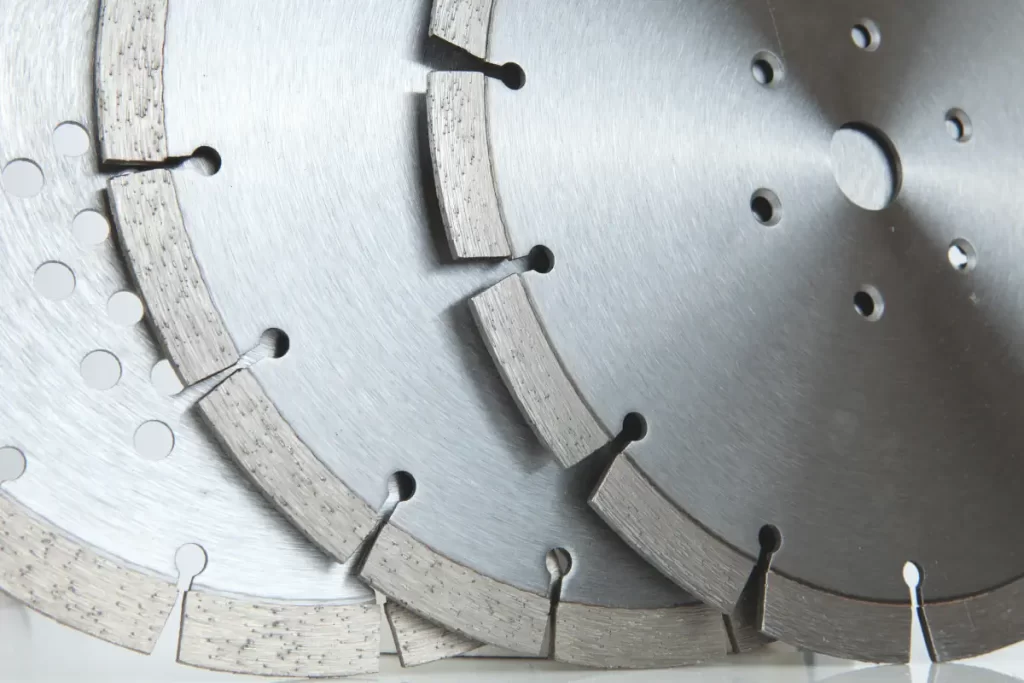
The Future for the World’s Hardest Material
In conclusion, Dr. Zhan, Moellendick, Dr. He, and their colleagues have successfully created and tested a record-breaking polycrystalline diamond compact material using their newly developed ultra-high pressure and high-temperature technology.
Although this technology represents a huge breakthrough, one area for future work still remains. Currently, the team’s ultra-high pressure and high-temperature technology is not yet available on a large commercial scale. Therefore, the researchers plan to conduct further research in order to scale up their technology, so that scientists, manufacturers, and engineers in diverse disciplines and industries can gain access to the world’s hardest material.
Meet the researchers
Timothy E. Moellendick
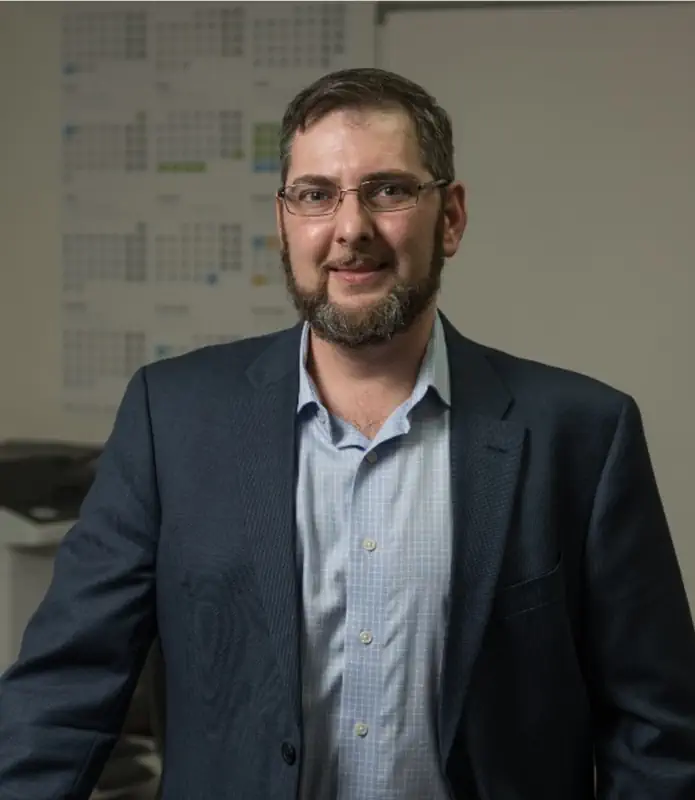
Timothy E. Moellendick achieved his BS in Petroleum Engineering from Marietta College in 1996. Currently, he is the Chief Technologist for the Drilling Technology Division at Saudi Aramco’s EXPEC Advanced Research Center.
Moellendick is considered the industry expert in casing and liner drilling applications and engineering, with more than 25 years of oil and gas industry experience.
In his previous role as Director of Technology for Schlumberger, he was responsible for growing the technical and operational knowledge base used to develop, plan, and execute technology worldwide.
Dr. Guodong (David) Zhan
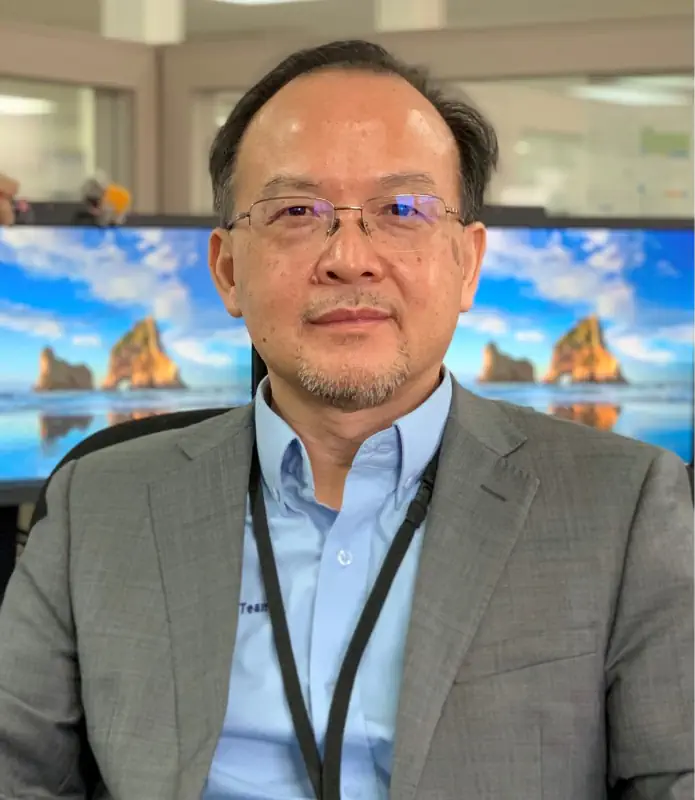
Dr. Guodong (David) Zhan earned his Ph.D. in Metallurgy Engineering from Huazhong University of Science and Technology, China.
He is a world-renowned materials scientist and drilling tools expert with an outstanding track record of advanced technologies from invention through to full commercialization.
Dr. Zhan’s influence spans academia and industry, from internationally renowned universities and laboratories such as the University of London, University California at Davis, National Institute for Materials Science in Japan, and Chinese Academy of Sciences, to global Fortune 500 companies such as Schlumberger.
He currently leads the advanced drilling tools team at Saudi Aramco’s EXPEC Advanced Research Center.
Dr. Zhan has received a number of prestigious academic and industrial awards. He serves as an international conference section chairman and technical committee member in professional societies and is a board member of a number of scientific journals.
Professor Duanwei He
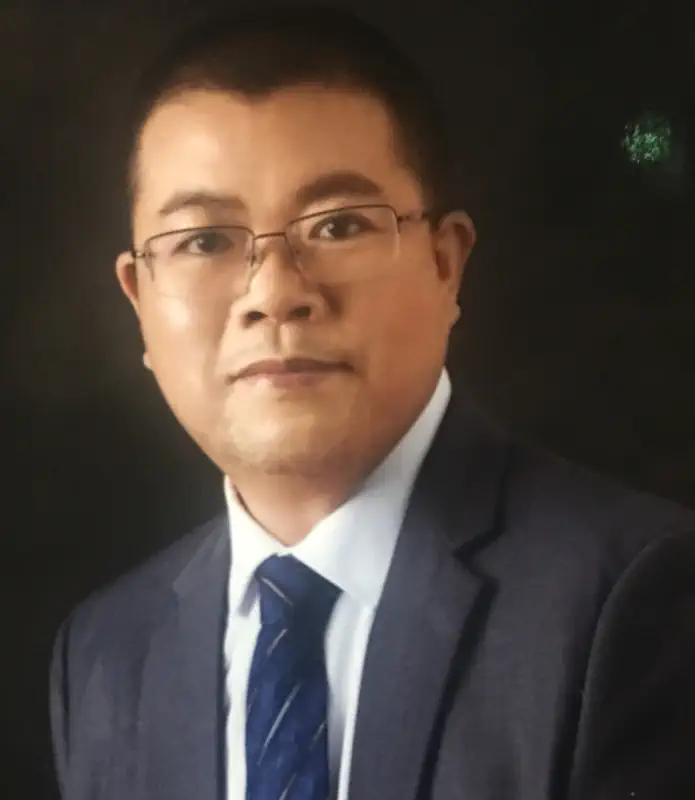
Dr. Duanwei He achieved his Ph.D. in Condensed Matter Physics from the Institute of Physics, Chinese Academy of Sciences, in 1998.
From 1999 to 2006, he worked at various prestigious institutions, including the National Institute for Materials Science in Japan, Los Alamos National Laboratory, Princeton University, and Schlumberger. In 2005, he began his current position as a professor and director of the Institute of Atomic and Molecular Physics at Sichuan University.
Dr. He is a world-renowned scientist and expert in hard materials and high-pressure physics.
Contact
Email: guodong.zhan@aramco.com
Funding
Saudi Aramco
Further Reading
Q Li, G Zhan, D Li, D He, TE Moellendick, CP Gooneratne, AG Alalsayednassir, Ultrastrong catalyst-free polycrystalline diamond, Scientific Reports, 2020, 10, 22020. https://doi.org/10.1038/s41598-020-79167-4
Source
This article originally appeared in Scientia, with the title of “Dr. Guodong (David) Zhan | Timothy Eric Moellendick | Dr. Duanwei He – Cutting-edge Technology: Developing the Hardest Material on Earth”.
- An Innovative Medium-Voltage DC Circuit Breaker for Renewable Power Grids - October 13, 2022
- Scientists are Mapping the Earth’s Magnetosphere with Energetic Atoms - September 30, 2022
- Scientists are Developing Recyclable and Self-healing Plastics - August 9, 2022